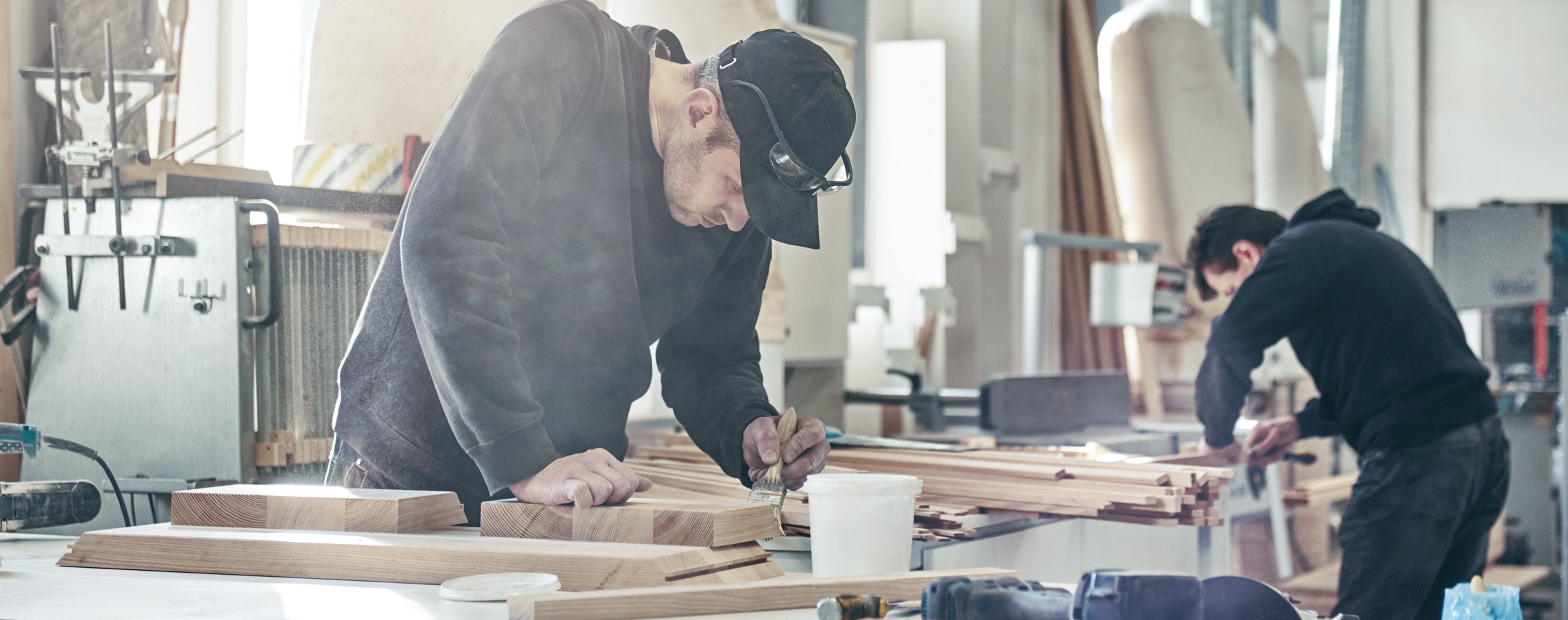
Duże ryzyko w sektorze przetwórstwa drewna przekłada się również na kwestie ubezpieczeniowe, a w szczególności techniczne podejście do tej gałęzi przemysłu. Stąd często pojawiają się oczekiwania dotyczące zabezpieczenia celem minimalizacji zagrożenia lub ograniczenia możliwych strat jakie mogą powstać w przypadku pożaru czy wybuchu.
Istotne zagrożenia dla obróbki drewna to przede wszystkim pożar oraz wybuch, które wymagają adekwatnych zabezpieczeń, o czym w dalszej części artykułu. Przemysł przetwórstwa drewna można podzielić na branże, gałęzie produkcji charakteryzujące się różną technologią procesu produkcji.
W pierwszej kolejności pojawia się obróbka tartaczna.
Kłoda pozyskana z gospodarki leśnej poddawana jest manipulacji, okorowaniu i kierowana do produkcji elementów tartacznych. W procesie szczególnym zagrożeniem jest pojawienie się metalowych elementów jak np. łuski po nabojach, gwoździe. Pozostawienie w kłodzie metalowych elementów skutkuje możliwością uszkodzenia urządzeń obróbczych (pił), co w konsekwencji prowadzi do powstania zarzewia ognia w postaci iskry.
Minimalizacja zagrożenia jest stosunkowo prosta. Służy do tego urządzenie w postaci detektora metalu. Każda kłoda przed obróbką powinna być sprawdzona przez detektor. Proces jest automatyczny, a urządzenie jest montowane przy taśmociągu kierującym kłodę do traka.
Kolejnym na tym etapie miejscem zagrożenia jest podtracze. Jest to miejsce gdzie ograniczony jest nadzór fizyczny, a samo miejsce charakteryzuje się znacznym nagromadzeniem palnych odpadów produkcji – trociny, pył. Stosowanie w tych strefach systemu sygnalizacji pożarowej jest oczekiwanym zabezpieczeniem pozwalającym na poprawę bezpieczeństwa i możliwą szybką reakcję służb technicznych. Odpowiednio dobrana instalacja będzie odporna na zapylenie i inne niekorzystne warunki panujące w tej strefie.
Kolejny proces to rozkrój na tarcicę budowlaną/ meblarską.
Wstępnym procesem obróbki jest cięcie drewna litego, np. za pomocą pił tarczowych, taśmowych albo panelowych, w zależności od specyfiki półproduktu i efektu, który ma zostać osiągnięty. Uzyskanym materiałem w tym etapie będzie tarcica w postaci desek, kantówki, listew, deszczułek.
Na tym etapie mamy zagrożenia wynikające z pylenia co wynika z mniejszych granulacji odpadów, pojawienia się większej ilości pyłów i trocin. Poziom ryzyka wynikać będzie również z rodzaju drewna (liściaste, iglaste) i stopnia wilgotności.
Zastosowanie systemu detekcji i gaszenia iskier pozwala chronić przed wybuchem i w konsekwencji pożarem strefy aspiracji i stacji filtrów, a w następnej kolejności parku maszynowego zakładu i całości mienia.
Istotą rozwiązania jest wykrycie przez moduł detekcji iskier (źródeł stanowiących o możliwości powstania zarzewia ognia) i automatyczne wyzwolenie gaszenia wodą (mgła wodna). Tym samym nie dopuszczamy do rozwinięcia się pożaru w przypadku powstania źródła energii w atmosferze wybuchowej.
W tej części produkcji również może być wymagane zastosowanie detekcji metali w przypadku ryzyka, gdy obrabiane drewno dostarczane jest od zewnętrznych podmiotów i brak jest możliwości weryfikacji zagrożenia w inny sposób.
Oczekiwanym zabezpieczeniem będzie również system sygnalizacji pożarowej SSP. Automatyczna sygnalizacja pożarowa niezależnie i bezzwłocznie wywoła alarm pożarowy. Pozwoli to na szybkie uruchomienie akcji ratowniczej, a w przypadku praktycznego przeszkolenia pracowników daje duże szansę na skuteczne ugaszenie pożaru już w pierwszych chwilach jego rozwoju.
Dlatego tak istotne są dla tych procesów adekwatne zabezpieczenia w postaci systemu wykrywania i gaszenia iskier w instalacjach aspiracji maszyn i urządzeń oraz ochrona strefy produkcji systemem sygnalizacji pożarowej SSP.
Kolejnym procesem produkcji po przygotowaniu formatki z elementów drewnianych jest poddawanie frezowaniu, wycinaniu albo toczeniu. Przy frezowaniu powierzchni drewna nadawany jest odpowiedni kształt odpowiadający geometrii ostrzy frezu lub wynikający ze ścieżki, po jakich się on przemieszcza. W ten sposób obrabiane są powierzchnie płaskie, ranty, a nierzadko także realizowane jest cięcie lub wycinanie. Na tym etapie możemy spotkać się również z procesem szlifowania.
Występujące zagrożenia są podobne do wymienionych wcześniej jednak ze zwiększonym zagrożeniem powstawania stref zagrożonych wybuchem. Procesy produkcji będą charakteryzowały się znacznym ryzykiem pojawienia się obłoków pyłu wybuchowego w miejscach obróbki, w strefach aspiracji. W związku z tym niezbędne jest przeprowadzenie Oceny zagrożenia wybuchem i zidentyfikowanie takich stref. Następnie wykonanie Dokumentu zabezpieczenia przed wybuchem celem weryfikacji zastosowanych rozwiązań, dobranych urządzeń do pracy w strefach wybuchowych. Dokumenty pozwolą ocenić ryzyko czy jest akceptowalne, zweryfikować prawidłowość dobranych urządzeń lub wymagać zastosowania dodatkowych zabezpieczeń w przypadku pojawienia się ryzyka wybuchu i możliwości powstania czynnika inicjującego wybuch.
Na tym etapie pojawiają się dodatkowe zagrożenia wymagające zabezpieczeń. Z zagrożeniem będziemy mieli do czynienia poza bezpośrednią strefą produkcji lub magazynowania. Takim przykładem jest stacja filtrów, a także silos z odpadami procesowymi. Urządzenia połączone są bezpośrednio z halą produkcji ale również z kotłownią czy brykieciarnią. Powstanie pożaru i wybuchu w stacji filtrów czy silosie często kończy się przeniesieniem pożaru i wybuchu do hali produkcji lub kotłowni. Dlatego istotne jest zabezpieczenie instalacji w klapy zwrotne, klapy odciążające, urządzenia redukcji wybuchu.
Każde z wymienionych urządzeń odpowiada i zabezpiecza mienie w inny sposób i stanowi o innym zakresie ochrony.
- Klapy odciążające
Klapy odciążające wybuch są urządzeniami wielokrotnego użycia, najczęściej stosowanymi w systemach filtracji i zbiornikach. W chwili wybuchu klapa ulega otwarciu uwalniając do atmosfery ciśnienie oraz płomienie, aby następnie samodzielnie się zamknąć. W ten sposób hamowany jest dopływ świeżego powietrza, co ogranicza ryzyko pożaru do jakiego może dojść we wnętrzu. Należy pamiętać, że wokół klap należy wyznaczyć jako strefy niebezpieczne w obrębie, której nie mogą znajdować trakty piesze, podesty, drogi czy też inne urządzenia.
- Klapy zwrotne
Zasada jej działania jest prosta i stosowana w przemyśle. Klapa zwrotna to wytrzymała na wysokie ciśnienie uchylna klapa zamontowana na zawiasach albo otwierana ciśnieniowo, pozwalająca otwierać się swobodnie w jedną stronę. W ten sposób klapa może przepuszczać materiał transportowany pneumatycznie w strumieniu powietrza. Jednocześnie w chwili wybuchu, ciśnienie skierowane w przeciwnym kierunku do przepływu materiału zamyka klapę uniemożliwiając rozprzestrzenianie się wybuchu.
Podobnym urządzeniem może być zasuwa szybkiego zadziałania klasyfikowane również jako system odsprzęgania wybuchu. Działa on podobnie jak typowe zasuwy nożowe z tą różnicą, że ich czas reakcji oraz zamknięcia jest ekstremalnie krótki. Są one aktywowane poprzez dynamiczne czujniki ciśnienia lub/i czujniki płomienia, a całością systemu zarządza dedykowana centrala sterująca.
- Izolacja wybuchu
To urządzenia redukcji wybuchu traktowane jako samoczynne instalacje przeciwwybuchowe. Urządzenia związane na stałe z urządzeniem technologicznym, których zadaniem jest wykrycie w bardzo wczesnej fazie wybuchu przez ograniczenie wzrostu ciśnienia w urządzeniu bądź jego stłumienie. Tyle mówi teoria.
Zabezpieczenie izolujące wybuch przed przedostaniem się do innych urządzeń jest systemem aktywnym. Podstawowa różnica to zadziałanie przed dotarciem do urządzenia wybuchu poprzez aktywne przeciwdziałanie rozprzestrzenianiu się wybuchu. Realizują to przez zamykanie jak najszybciej wszelkich kanałów, rur, czy przesypy, na których są montowane, natychmiast po wykryciu powstania wybuchu przez specjalne czujniki.
Ich działanie to system czujek wykrywający zagrożenie i reakcja przeciwdziałąjąca. Butle HRD mogą być wykorzystywane nie tylko jako system tłumienia wybuchu, ale również, jako niezwykle skuteczny, aktywny system izolacji wybuchu. Zamontowane w kanałach, rurach, czy przesypach butle HRD, kiedy zostaną aktywowane przez czujniki, natychmiastowo wtłaczają do tych kanałów proszek tłumiący, momentalnie zamykając takie kanały, nie pozwalając się wybuchowi dalej rozprzestrzeniać.
Poza zabezpieczeniami technicznymi niezmiernie istotne są również formalne uregulowania wynikające z przepisów prawa jak np. Rozporządzenie: Dz.U. 2010.138.931 z późniejszymi zmianami w sprawie minimalnych wymagań, dotyczących bezpieczeństwa i higieny pracy, związanych z możliwością wystąpienia w miejscu pracy atmosfery wybuchowej.
Stworzenie dokumentów Ocena ryzyka wybuchu i Dokumentu zabezpieczenia przed wybuchem przez zewnętrzną firmę posiadającą doświadczenie w ocenie ryzyka i analizie zagrożeń pozwoli na weryfikację stosowanych rozwiązań i urządzeń. Pozwoli na prawidłowy dobór urządzeń do istniejącego ryzyka i zastosowanie adekwatnych zabezpieczeń jak np. instalacje wyrównawcze, dobór klasy urządzeń i instalacji do występujących stref zagrożenia wybuchem.
Opracowana dokumentacja pozwoli na weryfikację istniejących zabezpieczeń pod kątem spełnienia Dyrektywy Atex.
Jednocześnie należy mieć na uwadze, że wszystkie wymienione zabezpieczenia działają lokalnie i skierowane są na lokalne ryzyka w danych fragmentach procesu.
W związku z powyższym dla ograniczenia wielkości szkody mogą być konieczne do zastosowania stałe urządzenia gaśnicze – zwane potocznie instalacjami tryskaczowymi.
Inną możliwością może być podziału całości zakładu na osobne ryzyka, osobne strefy pożarowe np. przez wydzielenie pożarowe powierzchni produkcji i składowania/ magazynowania.
Optymalnym rozwiązaniem jest organizacja procesu w osobnych strefach pożarowych.
Istotna w tym przypadku będzie klasa odporności ścian oddzielenia pożarowego oraz techniczne wykonanie oddzielenia w konstrukcji obiektu. Wynika to bezpośrednio z wysokiego obciążenia ogniowego dla tego rodzaju działalności – składowanie palnych materiałów. Dlatego ważne jest by konstrukcja ścian była wykonana w technologii odpornej na działanie ognia, przede wszystkim ściany murowane, żelbetowe dopiero w drugiej kolejności ściany wykonane z płyt warstwowych z rdzeniem z wełny mineralnej. Ściany oddzielenia pożarowego winny mieć klasyfikację minimum REI 120, co może skutecznie oddzielić strefy pożarowe.
W każdym przypadku realizacji tego typu rozwiązań zalecamy zawsze kontakt z inżynierami oceny ryzyka TUiR WARTA. Nasi inżynierowie pomogą w opracowaniu rozwiązań podziału na strefy pożarowe w zakładzie, a także koncepcji wykonania instalacji zabezpieczenia pożarowego.
Jeżeli natomiast interesują Was dodatkowe informacje dotyczące tego tematu, zapraszamy do kontaktu z Rafałem Biernackim: rafal.biernacki@warta.pl.