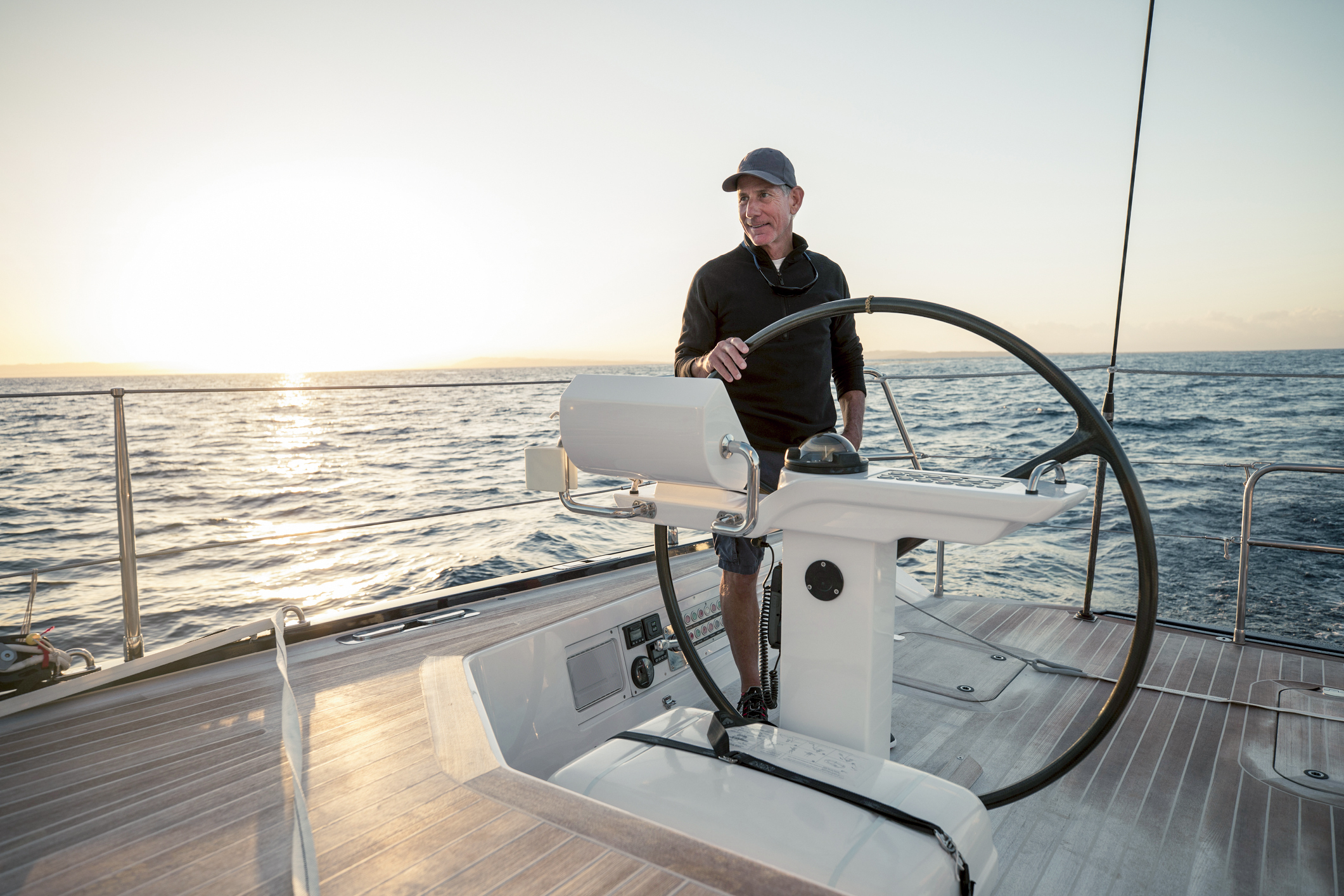
Laminaty to tworzywa powstałe z połączenia włókien z lepiszczem, który stanowi najczęściej roztwór żywicy w styrenie. W procesie produkcji wykorzystuje się wiele czynników chemicznych, takich jak:
- aceton,
- nadtlenek dikumylu,
- nadtlenek acetyloacetonu, dwuetyloanilina,
- sole kobaltu trójwartościowego.
Trochę historii
Laminaty mają wielowiekową historię, która zapoczątkowana została w Chinach, powstaniem materiału znanego nam jako laka. Wytwarzana ona była przez pokrywanie cienkiego papieru lub tkaniny (zwykle wielu warstw) sokiem z rośliny rodzaju sumak Rhu. Sok z tej rośliny posiada właściwość samoutwardzania, który w połączeniu ze „zbrojeniem” daje materiał o wysokiej wytrzymałości.
Prawdziwy rozwój produkcji laminatów (kompozytów), na skalę przemysłową, miał miejsce pod koniec II wojny światowej. Początkowo stosowano je głównie w elektrotechnice oraz radiotechnice, jako materiał zwany bakelitem. Jest to syntetyczne tworzywo sztuczne, wykonane z wielu warstw płótna nasyconych termoutwardzalną żywicą. Obecnie materiał ten odchodzi w zapomnienie, ze względu na swoje właściwości (sztywność, łamliwość, szybkie starzenie) i brak zainteresowania potencjalnych odbiorców.
Dowodem na to, że prace nad laminatami i ich szybki rozwój sięga pierwszej połowy XX w. jest m.in. poradnik pt. „Tworzywa sztuczne”. Pierwsze wydanie tej pracy ukazało się w Berlinie w 1936 r. Autorem tego dzieła jest doktor F. Past. Poradnik miał upowszechniać wiedzę na temat tworzyw sztucznych wśród różnych grup zawodowych: dyrektorów zakładów, konstruktorów, nabywców, użytkowników i robotników. Od tego czasu, a szczególnie od lat 50. ubiegłego wieku, powiększał się asortyment surowców chemicznych, wykorzystanych m.in. w przetwórstwie żywic. Miało to znaczący wpływ na rozwój nowoczesnych technologii produkcji żywic poliestrowych i łączenia ich z włóknami takimi, jak np.: włókna szklane, węglowe. Sposób łączenia żywicy z tkaniną szklaną umożliwił wytwarzanie konstrukcji o krótkich seriach produkcji, czasami i jednostkowych egzemplarzy. Technologia stosowana przy produkcji wyrobów kompozytowych jest na tyle elastyczna, że pozwala na sterowanie procesem, w celu uzyskania produktu zgodnego z zamówieniem klienta, tak pod względem kształtu, jak również parametrów fizycznych i chemicznych. Współczesne laminaty zostały poprzedzone produkcją półfabrykatów płytowych, wykonanych z kilku warstw prasowanego papieru nasyconego żywicą melaminową, stosowaną kiedyś do produkcji mebli.
Laminaty – co to jest?
Laminaty są to tworzywa powstałe z połączenia włókien z lepiszczem. Włókna stanowią konstrukcję a lepiszcze, będące najczęściej żywicą, scala i łączy włókna. Doskonała przyczepność żywic do włókna powoduje, że powstały w ten sposób produkt charakteryzuje się m.in. znaczną wytrzymałością mechaniczną, niewielkim ciężarem właściwym czy odpornością na korozje. Nie wymaga również skomplikowanych technologii i metod otrzymywania. W produkcji laminatów stosuje się żywice o różnych właściwościach, np.: żywice poliestrów nienasyconych (UP), żywice epoksydowe (EP) czy żywice fenolowe (PF). Specyficzne właściwości posiadają żywice specjalne tzw. niepalne. Należy jednak pamiętać, że nie jest to całkowita niepalność. Żywice te palą się, gdy jest źródło ognia podtrzymujące palenie. „Niepalność” jest wynikiem dodania środków tłumiących ogień.
Proces technologiczny produkcji laminatów umożliwia sterowanie parametrami takimi jak:
- wytrzymałość na ciśnienie wewnętrzne pochodzące od medium,
- wytrzymałość na zmiany kształtu wywołane zewnętrznymi siłami,
- odporność na określone czynniki agresywne,
- odporność na ścieralność (rurociągi, osadniki, zbiorniki, wanny itp.).
Jedynie wyobraźnia ogranicza możliwości wykorzystania laminatów. W celu urozmaicenia wyglądu laminatów, nadania im indywidualnego wyrazu stosuje się różne kolorystyczne odmiany. Ale skąd ta różnorodność kolorystyczna laminatów? Efekt ten uzyskuje się poprzez dodawanie pigmentów do żelkotu nakładanego jako warstwa powierzchniowa wytwarzanego produktu.
Zastosowanie laminatów
Wytwarzane laminaty mają różne zastosowanie, które obecnie jest uzależnione od potrzeb klientów. Produkowane są obecnie następujące wersje laminatu:
- jednostronny – jedna strona dekoracyjna,
- dwustronny – dwie strony dekoracyjne,
- standardowy – do oklejania powierzchni płaskich, do produkcji parapetów i blatów,
- trudnozapalny – wykorzystywany w budynkach użyteczności publicznej,
- podłogowy – do produkcji paneli podłogowych,
- iluminat – laminat świecący do wystroju wnętrz,
- techniczny – stosowany jako materiał m.in. elektroizolacyjny,
- kompaktowy – do produkcji urządzeń sklepowych,
- elewacyjny ‐ elewacje budynków,
- inne – do wypełnień np.: drzwi i balustrad.
Jednak największe zastosowanie laminatów występuje w przemyśle budowy jednostek pływających, ze względu na ich właściwości, takie jak: wodoszczelność, wytrzymałość mechaniczna, odporność na korozję.
Potrzeby klientów określają, jakie materiały (np. żywice) muszą być zastosowane dla osiągnięcia produktu z laminatu. Wielość zastosowań laminatów spowodowała, że stosuje się je zarówno na skalę przemysłową, jak i amatorską. Na przykład:
- żywice poliestrowe najczęściej stosowane są w przetwórstwie, do produkcji m.in.: artykułów sportowych, łodzi, szybowców, samolotów, elementów karoserii pojazdów samochodowych (od osobowych do ciężarowych), pojemników, mebli, konstrukcji wielkoprzestrzennych np. obudowy generatorów elektrowni wiatrowych.
- żywice epoksydowe – stosowane są w produkcji elementów o zwiększonych parametrach wytrzymałości mechanicznej, termicznej i chemicznej, np. zbiorniki wysokociśnieniowe, elementy rurociągów.
- żywice fenolowe – znajdują zastosowanie w produkcji elementów o zwiększonych parametrach bezpieczeństwa pożarowego.
Odporność na działanie czynników zewnętrznych (np. korozję) powoduje, że konstrukcje z laminatów mają perspektywy nowych zastosowań. Przykładem takich konstrukcji są obecnie wytwarzane rury z laminatów, które mają różne przeznaczenie – od słupów oświetleniowych do rur do przesyłania niebezpiecznych czynników chemicznych.
Surowce stosowane przy produkcji laminatów
Aby zabezpieczyć zewnętrzne warstwy laminatów przed negatywnym działaniem czynników atmosferycznych, uszkodzeniami mechanicznymi oraz podnieść estetykę wyrobu i nadać pożądany kolor i połysk, stosuje się tzw. żelkot. Stanowi on mieszaninę stabilizowanego roztworu żywicy poliestrowej w styrenie z dodatkiem barwników. Styren stanowi do 30% masy żelkotu.
W produkcji laminatów włókno szklane stosowane jest w postaci mat, tkanin, mato tkanin, taśm rowingowych. W procesie produkcji laminatów stosowane są żywice powłokowe (utwardzane na zimno) zawierające dodatki takie, jak parafina, która w procesie produkcji wydziela się na powierzchni. Parafina redukuje emisję styrenu oraz eliminuje kleistość powierzchni utwardzonej. Tworzenie stałej masy jest procesem sieciowania przestrzennego, które następuje w wyniku reakcji chemicznych grup funkcyjnych zawartych w żywicy z odpowiednim utwardzaczem. Poza głównymi składnikami takimi jak żywica poliestrowa i włókna szklane, podczas produkcji występują także takie składniki, jak: inicjatory polimeryzacji, przyśpieszacze, inhibitory oraz wypełniacze (np. kreda, wodorotlenek glinu).
Stosowane inicjatory polimeryzacji, przyśpieszacze mają w większości przypadków właściwości żrące. Należy pamiętać, że proces polimeryzacji jest związany z obecnością inicjatora polimeryzacji oraz przyśpieszacza. Przyśpieszaczem regulujemy czas twardnienia (żelowania). Gotowe produkty muszą posiadać odpowiednie parametry techniczne zgodnie z zapotrzebowaniem złożonym przez klienta. Równocześnie, należy mieć na uwadze, czas potrzebny do twardnienia powłok. W tym celu, używa się inicjatorów, przyśpieszaczy. Ważnym materiałem w produkcji laminatów są środki, oddzielające, bez których niemożliwe byłoby oderwanie produktu od formy. Środki oddzielające występują w dwóch typach: w stałym i płynnym. Przy pracach z bezwodnikami kwasów organicznych należy zwrócić uwagę na zagrożenie, wynikające z ich właściwości fizycznych i chemicznych. Szczególnie te lotne lub sublimujące mogą stanowić zagrożenie dla zdrowia, powodując m.in. uszkodzenie wzroku. Pasty nadtlenkowe i przyśpieszacze aminowe (aminy trzeciorzędowe) zaklasyfikowane są jako żrące, nadtlenki ulegają rozkładowi przy nieprawidłowym przechowywaniu – narażenie na wysoką temperaturę, promienie słoneczne.
To tyle jeśli chodzi o opisanie czym są laminaty. W drugiej części artykułu (dostępnym już w czerwcu) przejdziemy do omówienia zasad bezpiecznego postępowania z tym surowcem.
Zaczniemy od zasad postępowania z surowcami do produkcji laminatów. Ze względu na właściwości chemiczne poszczególnych składników, jakie są dodawane do żywic (celem ich utwardzenia w procesie polimeryzacji), roztwory żywic mogą być przechowywane z dodatkiem przyśpieszaczy. Producenci zalecają stosowanie przy produkcji laminatów żywic z wmieszanym przyśpieszaczem – są to tzw. żywice preakcelerowane, które są dodawane i mieszane bezpośrednio przed użyciem w produkcji. Mieszanie tych składników powinno być wykonywane w wydzielonym miejscu hali produkcyjnej lub magazynie wyposażonym w wentylację zapewniającą bezpieczne warunki pracy.
Proces produkcji wyrobów z laminatów
Produkcja wyrobów z laminatów poliestrowo‐szklanych jest stosunkowo prostą metodą, która pozwala na aktywną kontrolą nad tym procesem. Parametry produktu można dostosować do potrzeb klienta, w tym m.in. dopasować:
- wytrzymałość na ciśnienie (wewnątrz zbiorników i rurociągów),
- wytrzymałość na odkształcenia,
- odporność na warunki atmosferyczne, jak również na czynniki agresywne (w tym kwasy i zasady).
W tym ostatnim przypadku użytkownik musi podać jakiego rodzaju środki chemiczne będą miały kontakt z laminatem, co pozwoli określić, jakiego rodzaju żywic należy użyć do produkcji.
Ze względów ekonomicznych do produkcji większości laminatów stosuje się żywice poliestrowe. Technologia zakłada układanie na formie krzyżujących się warstw mat i tkanin szklanych. Inne metody produkcji laminatów to:
- metoda bezciśnieniowa formowania ręcznego, przeciągania i nawijania,
- metoda próżniowa, niskociśnieniowa,
- metoda ciśnieniowa, przy użyciu elastycznego worka,
- metoda nawijania lub prasowania w ogrzewanych formach.
Najczęściej wykorzystywaną metodą jest bezciśnieniowa metoda formowania ręcznego. Tak prowadzony proces technologiczny jest prosty i nie wymaga specjalistycznego wyposażenia. Proces ten polega na ręcznym nanoszeniu żywicy poliestrowej z dodatkiem inicjatora z przyśpieszaczem na ułożone na formie warstwy mat szklanych. Maty powinny być ułożone w krzyżujące się warstwy, a żywicę nanosi się np. pędzlem lub wałkiem. Formy mogą być wykonane z różnych materiałów: od drewna, przez glinę, gips, metal, do form z laminatów. Metoda ta jest powszechna w przemyśle stoczniowym. Popularne jest również stosowanie metody natryskiwania na formy. W tej metodzie zawartość szkła w laminacie wynosi ok. 30 proc.
Proces produkcji laminatów składa się z następujących czynności:
- ręczne nałożenie separatorów na formę (zabezpieczenie przy użyciu separatorów wosków stałych lub płynnego środka rozdzielającego przed przyklejeniem żelkotu do formy),
- ręczne lub natryskowe nałożenie żelkotu,
- nakładanie warstw zbrojenia (mat lub tkanin szklanych) i przesycanie ich żywicą lub natrysk sieczki szklanej przesycanej żywicą,
- wzmacnianie konstrukcji laminatu np.: wklejanymi elementami drewnianymi (najczęściej sklejka) lub metalowymi,
- utwardzanie,
- oderwanie od formy („odformowanie”),
- wykończanie wyrobów z laminatu, m.in.: obcinanie naddatków technologicznych i wycinanie (wiercenie) otworów,
- szlifowanie i polerowanie wewnętrznej strony laminatu.
Postępowanie w przypadku pożaru
Laminaty poliestrowo-szklane są materiałami łatwopalnymi. Opary tworzą mieszaniny wybuchowe z powietrzem. Pary są cięższe od powietrza i gromadzą się w dolnych częściach pomieszczeń.
Dlatego w przypadku pożaru należy usunąć z obszaru zagrożenia wszystkie osoby niebiorące udziału w likwidowaniu awarii. Konieczne jest również wezwanie Straży Pożarnej i Policji.
Do ugaszenia pożaru stosuje się środki gaśnicze w postaci dwutlenku węgla, proszku gaśniczego, piany średniej i ciężkiej oraz prądów wodnych rozproszonych Nie stosuje się natomiast zwartych strumieni wody na powierzchnię palącej się cieczy. Ponadto:
- w przypadku małego pożaru gaszenie może odbywać się za pomocą gaśnicy proszkowej lub śniegowej (dwutlenek węgla);
- jeśli mamy do czynienia z dużym pożarem, palące się zbiorniki lub rozlewiska gasimy pianą lub prądami wodnymi rozproszonymi. Zbiorniki narażone na działanie ognia lub wysokiej temperatury powinny być chłodzone wodą z bezpiecznej odległości. Dodatkowo, jeśli to możliwe, powinny zostać usunięte z obszaru zagrożenia (groźba wybuchu). Nie można również dopuścić do przedostania się ścieków po gaszeniu pożaru do kanalizacji i wód.
Odpowiednie warunki pracy
Ze względu na specyfikę stosowanych materiałów, a szczególnie zagrożenia pożarowo‐wybuchowe, produkcja laminatów powinna odbywać się w specjalnie przeznaczonej i wydzielonej części hali produkcyjnej. Oddzielenie to powinno być skuteczne i zabezpieczać przed przedostawaniem się na inne stanowiska pracy niebezpiecznych substancji uwalnianych do środowiska pracy podczas laminowania. Stanowiska, na których jest prowadzone laminowanie powinny posiadać właściwy system ogrzewania i wentylacji. Niedopuszczalne jest ogrzewanie hali produkcyjnej przy pomocy pieca z otwartym paleniskiem usytuowanym na hali lub w jej bezpośrednim sąsiedztwie. Bezpieczny sposób ogrzewania stanowisk pracy to nawiew ciepłego powietrza, w sposób zapewniający prawidłową realizację procesu produkcji oraz komfort pracy. W trakcie laminowania następuje uwalnianie się dużych ilości styrenu i acetonu. Ze względu na różnorodność formowanych kształtów oraz ręczne nakładanie żywicy, pracownik jest bezpośrednio narażony na te łatwolotne substancje chemiczne. Jest to również związane z technologią procesu, gdyż pracownik jest prawie stale obecny przy wykonywanym elemencie – zarówno gdy nakłada żywicę, jak i gdy ona wysycha. W czasie odparowywania rozpuszczalnika pracownik nakłada maty szklane, wprasowuje je w żywice, przebywając w obszarze o zwiększonym stężeniu tych substancji. Niezbędne jest korzystanie przez pracownika ze środków ochrony indywidualnej, chroniących układ oddechowy. Zagrożenie pożarowo‐wybuchowe związane jest również z obecnymi w procesie produkcji laminatów inicjatorami oraz przyśpieszaczami. Nieprawidłowe obchodzenie się z nimi może doprowadzić do pożaru, wybuchu oraz zniszczenia żywicy. Mowa o ich wspólnym składowaniu, przechowywaniu inicjatorów w opakowaniach po przyśpieszaczach i odwrotnie, niekontrolowanym ogrzewaniu, mieszaniu w nieprawidłowych ilościach i proporcjach. Mycie i czyszczenie narzędzi w rozpuszczalnikach (np. aceton) oraz ich suszenie musi odbywać się na oddzielnym stanowisku poza obszarem laminowania.
Podstawowe zasady bezpieczeństwa podczas produkcji laminatów
- zastosowanie systemu wentylacji wymuszonej przy posadzce hali produkcyjnej (opary styrenu są cięższe od powietrza),
- skuteczna instalacja uziemiająca (wyeliminowanie zagrożenia powstania przeskoku iskry),
- wydzielony pożarowo magazyn chemiczny (surowce palne).
Jeżeli jesteście zainteresowani dodatkowymi informacjami, to zapraszamy do kontaktu z Wiesławem Kameckim z Biura Oceny Ryzyka Technicznego (wieslaw.kamecki@warta.pl).